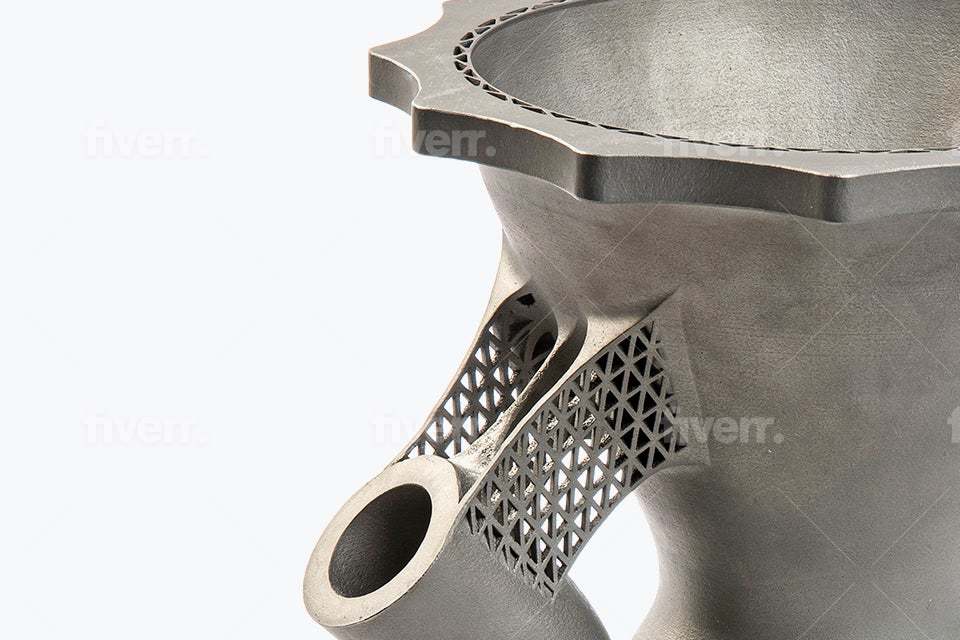
3D Metal Printing - The Revolution of Traditional Manufacturing Systems
Share
Metal 3D printing, unlocking a new industrial era
Over the past decade, metal 3D printing technology has emerged as a revolutionary advancement in the manufacturing industry. Gone are the days when the manufacturing of metal parts required expensive and time-consuming processes. With the ability to print three-dimensional metal objects precisely and efficiently, metal 3D printing has radically transformed the way metal components are conceived and produced.
One of the most intriguing aspects of this metal 3D printing is its versatility. Unlike traditional manufacturing methods, which often involve cutting or shaping solid materials, 3D printing allows the creation of complex objects from digital files. This digital data-driven approach offers unprecedented flexibility in the design and manufacturing of metal parts, resulting in more precise and customized end products.
3D printed metal technology has become an invaluable tool in a wide range of industries, from aerospace to medical. In the aerospace industry, for example, the ability to print lightweight, strong metal components has paved the way for the development of more efficient and cost-effective aircraft. Similarly, in the medical industry, metal printing has facilitated the manufacturing of customized implants and innovative medical devices, improving the quality of life of patients.
In addition to its usefulness in the manufacturing of final products, this technology is also transforming the prototyping and product development processes. Previously, prototyping metal parts required expensive tooling and molds, as well as long wait times. Now, with 3D printing, designers can create and test prototypes quickly and inexpensively, accelerating the product development cycle and allowing for faster, more efficient iteration.
Many advantages, but there are also complexities
Despite its many advantages, metal 3D printing also presents unique challenges. The quality and strength of 3D printed parts can vary depending on a number of factors, such as the type of material used, the printing process, and manufacturing parameters. Additionally, 3D printed metal technology still faces limitations in terms of the size and scale of objects that can be printed, as well as the cost of materials.
As metal 3D printing technology continues to evolve, these challenges are likely to be gradually overcome. Steady advances are being made in printing materials, manufacturing processes, and software design, which is expanding the capabilities and applications of metal 3D printing. In the future, we may see this technology used to manufacture an even wider range of products, from car parts to heavy machinery components.
3D metal printing technology represents a revolution in traditional manufacturing systems. With its ability to create complex metal objects quickly, accurately and customarily, metal 3D printing is transforming the way metal products are conceived and produced in a wide variety of industries.
The metals that are most frequently printed in 3D
As this technology continues to evolve, certain metal elements stand out for their popularity and applications in 3D printing. Here's an overview of some of the most commonly 3D printed metal elements:
- Stainless Steel : It is one of the most popular materials for metal 3D printing due to its durability, corrosion resistance, and versatility . 3D printed stainless steel is used in a wide range of applications, ranging from machinery parts to medical components.
- Aluminum : Aluminum is known for being lightweight and strong , making it a popular choice for 3D printing. It is used in the manufacturing of aerospace, automotive and consumer parts due to its excellent strength-to-weight ratio and thermal conductivity.
- Titanium : Titanium is highly valued for its corrosion resistance and excellent resistance to extreme temperatures . It is used in applications where high strength and rigidity is required, such as in the aerospace and medical industries. Titanium 3D printing enables the manufacturing of complex, lightweight components that would be difficult to achieve with traditional manufacturing methods.
- Nickel Alloys : Nickel alloys, such as Inconel, are known for their resistance to high temperatures and corrosion , making them ideal for applications in demanding environments, such as aircraft engines and gas turbines. 3D printing enables the manufacturing of intricate, heat-resistant components that are difficult to achieve with other manufacturing methods.
- Cobalt Chromium : This alloy is known for its biocompatibility and corrosion resistance , making it ideal for medical applications, such as the manufacturing of orthopedic and dental implants. Cobalt chromium 3D printing enables the production of customized medical devices that perfectly fit the individual needs of patients.

Printatonic offers 3D printing services tailored to your specific needs. With a team of experts in cutting-edge technology, we can transform your designs into resistant metal objects, with maximum precision and efficiency.